

It’s often the case that organisations experience workload spikes and down time.Īllocating human resources according to need can help to reduce costs. Instead, you can utilise technology to better understand when there is demand for any given job duty. However, expecting and measuring progress and efficiency based on an employees’ input time, rather than measuring outputs may prove fruitless. When you think of a corporate setting, tradition has dictated that employees should be working from 9-5. Through automation, you can immediately reduce errors (save time and money), streamline processes, and eliminate key person dependencies. In turn, employees can allocate their time to high value tasks, instead of repetitive and data-heavy duties.įurthermore, intelligent automation can be applied, which combines robotic process automation with machine learning so that the computer itself can make logical decisions based on the ability to spot patterns and trends.
Efficiency in operation manual#
Businesses can leverage robotic process automation (which is at the heart of many software solutions) to take over manual and tedious processes from humans. Automating to Reduce Manual Processes:Īutomation exists in several forms.
Efficiency in operation how to#
Organisations and teams have many opportunities when it comes to how to improve operational efficiency.įrom implementing automation solutions to leveraging data, let’s review some of the tried and true ways to make it happen. Consider applying operations research to find the quickest/most cost effective way to move goods from point A to point B and deploying creative solutions to reach levels of efficiency. Software analysis can be used to boost efficiency in distribution channels. One way to better manage inventory is to utilise predictive analysis and forecast future demand based on historical data. Inventory costs money to hold onto and move.įor operational efficiency to occur, there must be proper management and balance to have enough inventory to meet consumer demand, but not too much to misallocate capital. there’s risk associated with holding onto inventory). Inventory is considered to be an asset on a balance sheet, but it can end up becoming an operational liability (i.e.
Efficiency in operation free#
By automating processes, you can free up employees’ time, expedite production and reduce costs. Even if you work in an industry that is not manufacturing, you’re likely carrying out time-consuming processes. With the money and time you invest in creating an output, you’ll look to optimise processes and equipment.Ī surefire way to make this happen is by automating processes. Importantly, any business that operates in manufacturing will need to focus on production to accomplish operational efficiency. Without automation, finance processes are generally time-consuming, error-prone and have high opportunity costs.īy utilising financial automation tools, businesses can optimise their resource allocation, freeing up employees’ time to focus on high level task and achieve operational efficiency. To illustrate, finance teams often use the input of data to create the output of financial statements and/or information that’s needed for decision-making. By allocating resources optimally, you can eliminate waste and maximise revenue. Organisations rely on both human resources and material inputs to create their services and/or products. The following four aspects are the most critical for businesses to properly manage if they hope to achieve operational efficiency. What are the Factors of Operational Efficiency?Īpplying an operational efficiency strategy can be done by categorising and reviewing operations. Automation software can collect, process and translate all data into easily understandable reports that aid in better decision-making.
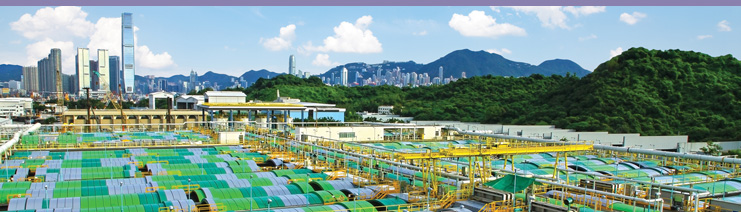
Benchmarking: Start by creating a benchmark of your team or organisation’s performance.3 Steps to Achieve Operational EfficiencyĪny organisation with the goal of being operationally efficient can do so by keeping in mind the following to-do’s, or actionable steps.
